Comprehensive Overview: What is Porosity in Welding and Just How to avoid It
Comprehensive Overview: What is Porosity in Welding and Just How to avoid It
Blog Article
Untangling the Enigma of Porosity in Welding: Tips for Lessening Issues and Taking Full Advantage Of Quality
In the intricate world of welding, porosity stays a persistent obstacle that can significantly influence the quality and integrity of bonded joints. Comprehending the factors that add to porosity formation is essential in the pursuit of remarkable welds. By untangling the mystery of porosity and carrying out effective approaches for problem minimization, welders can elevate the standards of their work to achieve exceptional quality results. As we dive into the midsts of porosity in welding, uncovering the keys to its prevention and control will certainly be vital for specialists looking for to understand the art of top quality weldments.
Comprehending Porosity in Welding
Porosity in welding, an usual issue experienced by welders, describes the existence of gas pockets or spaces in the welded product, which can jeopardize the honesty and top quality of the weld. These gas pockets are typically trapped throughout the welding process because of numerous variables such as inappropriate shielding gas, polluted base products, or inaccurate welding parameters. The formation of porosity can weaken the weld, making it at risk to splitting and rust, ultimately bring about architectural failings.
Understanding the source of porosity is essential for welders to efficiently prevent its incident. By identifying the importance of maintaining correct gas securing, making certain the sanitation of base materials, and maximizing welding setups, welders can substantially reduce the likelihood of porosity development. Additionally, using techniques like preheating the base product, utilizing correct welding techniques, and conducting complete examinations post-welding can better help in minimizing porosity problems. On the whole, an extensive understanding of porosity in welding is essential for welders to create top notch and long lasting welds.
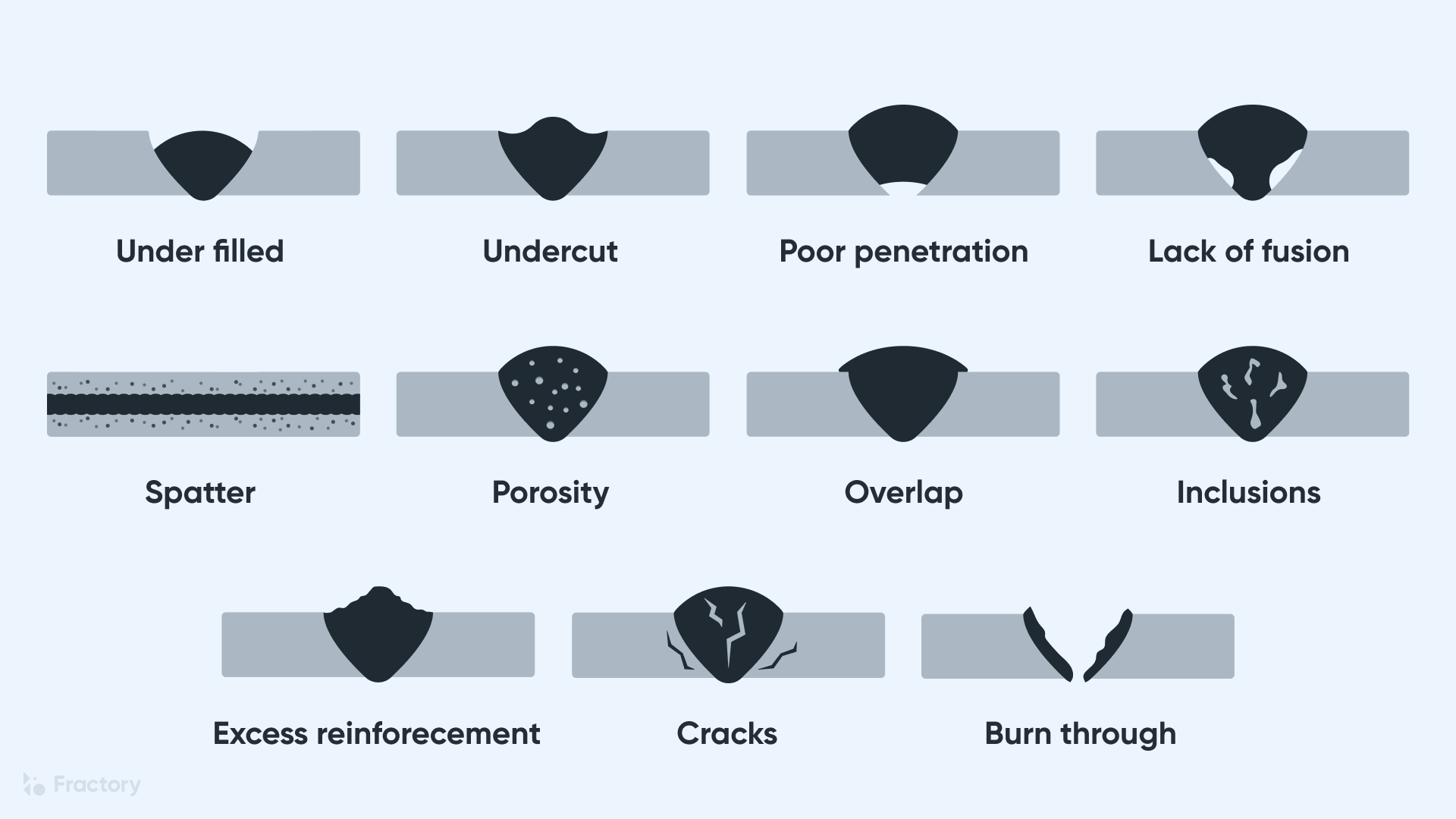
Usual Reasons For Porosity
When examining welding processes for prospective high quality issues, understanding the usual causes of porosity is necessary for preserving weld integrity and protecting against structural failings. Porosity, defined by the visibility of cavities or gaps in the weld steel, can substantially jeopardize the mechanical residential or commercial properties of a bonded joint.
An additional common source of porosity is the visibility of dampness and impurities externally of the base metal or filler material. When welding materials are not appropriately cleansed or are revealed to high levels of moisture, the vaporization of these impurities throughout welding can produce gaps within the weld grain. Additionally, welding at inappropriate parameters, such as excessively high travel speeds or currents, can create too much disturbance in the weld swimming pool, capturing gases and creating porosity. By attending to these usual reasons with appropriate gas shielding, material preparation, and adherence to ideal welding parameters, welders can reduce porosity and boost the high quality of their welds.
Techniques for Porosity Prevention
Implementing effective safety nets is important in lessening the occurrence of my explanation porosity in welding procedures. One strategy for porosity avoidance is ensuring proper cleaning of the base steel before welding. Contaminants such as oil, oil, corrosion, and paint can result in porosity, so detailed cleansing using suitable solvents or mechanical approaches is vital.

An additional secret preventive measure is the choice of the right welding consumables. Using top notch filler products and shielding gases that appropriate for the base steel and welding process can substantially lower the danger of porosity. Furthermore, preserving appropriate welding parameters, such as voltage, existing, travel rate, and gas circulation price, is vital for porosity prevention. Differing the resource recommended settings can result in improper gas coverage and poor fusion, leading to porosity.
Furthermore, utilizing appropriate welding methods, such as maintaining a regular traveling rate, electrode angle, and arc size, can aid prevent porosity (What is Porosity). Ample training of welders to ensure they comply with best techniques and quality control treatments is also necessary in lessening porosity issues in welding
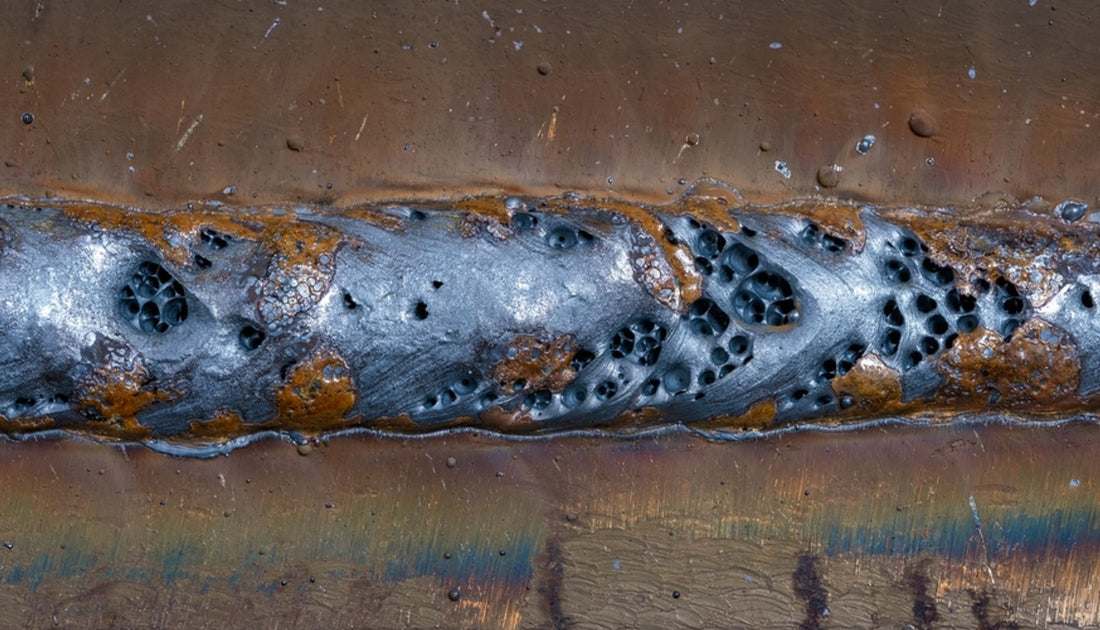
Finest Practices for High Quality Welds
Making sure adherence to sector criteria and correct weld joint preparation are fundamental facets of attaining constantly top quality welds. In addition to these fundamental actions, there are a number of best practices that welders can apply to better improve the high quality of their welds. One trick method is keeping correct sanitation in the welding location. Contaminants such as oil, grease, rust, and paint can adversely influence the high quality of the weld, leading to problems. Completely cleaning up the work surface and surrounding area prior to welding can aid reduce these problems.
An additional finest practice is to carefully select the ideal welding parameters for the particular products being signed up with. This consists of setting the correct voltage, current, take a trip speed, and shielding gas circulation price. Proper parameter choice ensures ideal weld penetration, combination, and general quality. Utilizing high-quality welding consumables, such as electrodes and filler metals, can dramatically affect the final weld high quality. Buying premium consumables can result in more powerful, more sturdy welds with less issues. By following learn the facts here now these best practices, welders can regularly generate top quality welds that fulfill industry standards and go beyond customer assumptions.
Value of Porosity Control
Porosity control plays a vital role in guaranteeing the integrity and top quality of welding joints. Porosity, identified by the existence of dental caries or gaps within the weld steel, can significantly compromise the mechanical residential properties and architectural integrity of the weld. Extreme porosity deteriorates the weld, making it more prone to cracking, corrosion, and total failing under functional loads.
Effective porosity control is necessary for maintaining the preferred mechanical homes, such as strength, ductility, and toughness, of the welded joint. What is Porosity. By minimizing porosity, welders can improve the general quality and reliability of the weld, ensuring that it meets the efficiency needs of the desired application
Additionally, porosity control is vital for attaining the preferred aesthetic appearance of the weld. Too much porosity not only compromises the weld however additionally interferes with its visual charm, which can be important in markets where appearances are essential. Correct porosity control strategies, such as using the correct shielding gas, regulating the welding criteria, and making sure appropriate sanitation of the base products, are necessary for generating premium welds with minimal problems.

Verdict
In final thought, porosity in welding is a typical flaw that can jeopardize the top quality of the weld. By recognizing the reasons of porosity and applying correct prevention techniques, welders can minimize issues and accomplish higher quality welds. It is necessary to manage porosity in welding to make sure the integrity and strength of the end product. Applying best practices for porosity control is critical for achieving optimum welding outcomes.
Report this page